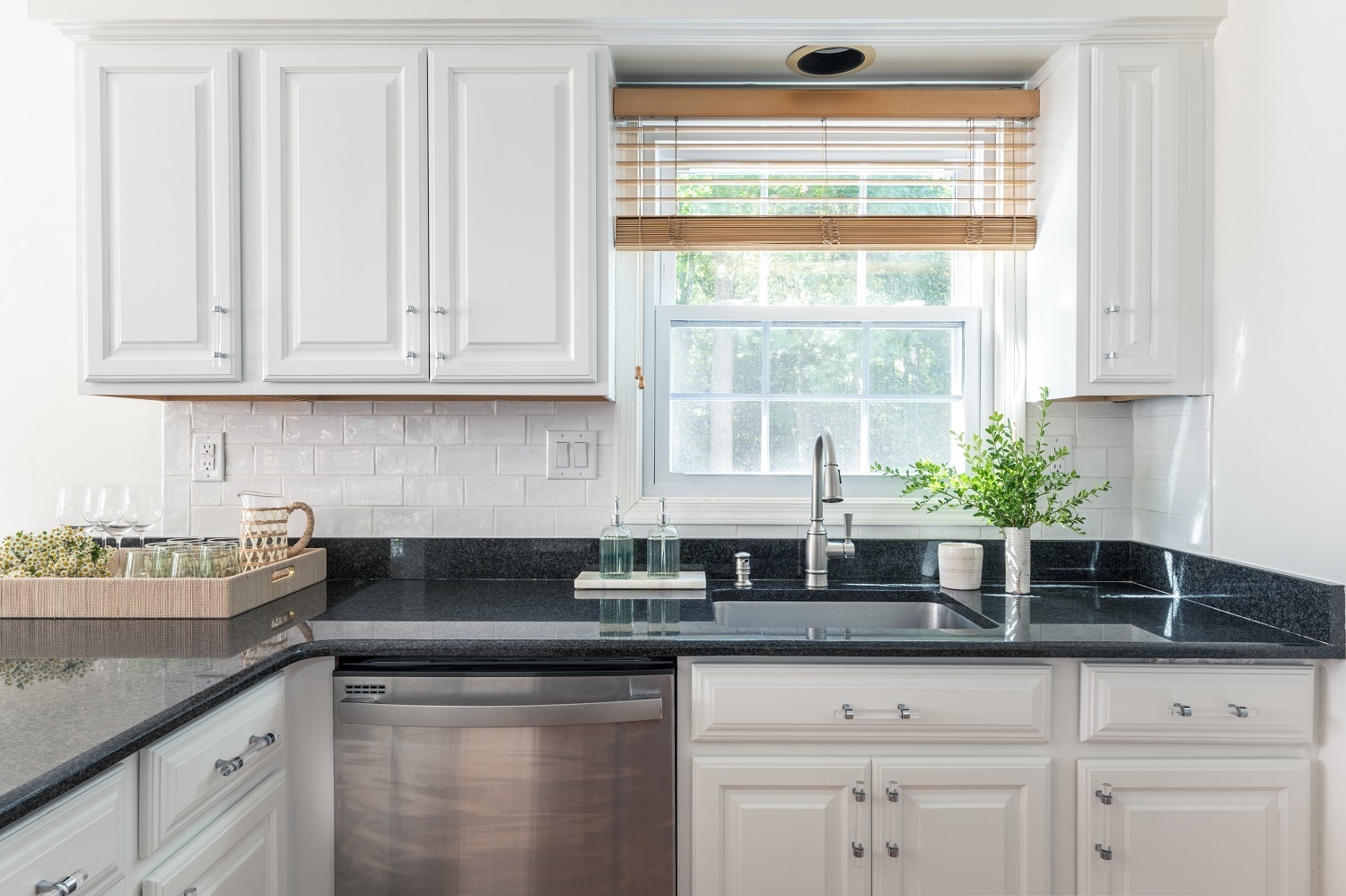
How much does a kitchen remodel cost? Find out the average cost and where you can save money on the path to building your ideal cooking space.
The average bus conversion cost ranges from $25,000 to $67,500, with most homeowners spending an average of $33,000. Key factors include bus type, materials, labor, and custom features.
Bus conversion costs depend on bus size, features, and finishes.
Labor, materials, and customizations are major cost drivers.
Professional labor makes up 40% to 60% of your total costs and is needed for electrical, plumbing, or finishing.
Expect to pay $200 to $400 per square foot for a professional bus conversion.
This article was created using automation technology and thoroughly fact-checked and edited by an Angi Editor in accordance with our AI policy.
Bus conversion costs are a major consideration for anyone dreaming of a custom mobile home. The average bus conversion cost is $33,000, with most projects ranging from $25,000 to $67,500 on average. Costs vary based on bus size, materials, and whether you DIY or hire a pro.
Expect to pay $200 to $400 per square foot, with professional labor rates ranging from $50 to $200 per hour, depending on the specialty.
Understanding the full scope of bus conversion costs means looking at every phase of the project. Costs include purchasing the bus, demolition and prep, repairs, insulation, flooring, plumbing, electrical, cabinetry, appliances, finishes, and furnishings. Basic conversions focus on essentials and cost less, while luxury conversions add custom work and premium materials.
Labor is a significant part of the budget—doing it yourself can save money, but hiring professionals ensures code compliance and quality, especially for complex systems.
Hidden costs can include unexpected repairs, delivery fees, or disposal of hazardous materials. It’s wise to set aside a contingency budget for surprises.
Project Phase | Description | Average Cost |
---|---|---|
Bus purchase | Buying a used or new bus | $3,000–$25,000 |
Demolition | Removing seats, flooring, fixtures | $1,000–$4,000 |
Structural repairs | Rust removal, frame, mechanical fixes | $1,000–$5,000 |
Insulation | Materials and installation | $150–$1,200 |
Flooring | Subflooring and finished floors | $450–$6,600 |
Plumbing | Tanks, lines, pumps, fixtures | $2,000–$6,400 |
Electrical | Wiring, panels, solar, batteries | $800–$4,000 |
Cabinetry | Custom kitchen, storage, built-ins | $1,000–$2,000 |
Appliances | Fridge, stove, heater, AC | $2,300–$5,000 |
Finishes | Walls, paint, trim, hardware | $2,500–$8,000 |
Furnishings | Bed, seating, table, storage | $1,000–$7,000 |
Labor | Professional installation and project management | $15,000–$60,000 |
Permits and fees | Inspections, DMV, building permits | $500–$3,000 |
Basic conversions stay near the lower end, mid-range conversions land in the middle, and luxury projects can exceed $100,000 with high-end finishes and systems. Labor can be 40% to 60% of your total bus conversion cost if you hire professionals.
The size of your bus is a major driver of bus conversion cost. Short buses (20 to 25 feet) are less expensive to convert than mid-size (25 to 35 feet) or full-size coach buses (up to 45 feet). Larger buses mean more square footage, which translates directly to higher material and labor costs.
You’ll pay $200 to $400 per square foot for a professional conversion. A small bus conversion is more budget-friendly but offers less living space, while a coach bus allows for more amenities at a higher price.
Bus Size (Sq. Ft.) | Description | Average Cost |
---|---|---|
Short (100–150) | Compact, easy to drive, limited space | $20,000–$40,000 |
Mid-size (150–200) | Balance of space and maneuverability | $30,000–$70,000 |
Full-size/coach (225–300) | Maximum living area, luxury options | $40,000–$100,000+ |
A short bus conversion may suit solo travelers or couples, while families or those wanting more comfort often opt for full-size coaches.
Many bus conversions rely on skilled professionals for specific tasks or full project management. Hiring a general contractor or project manager can cost 10% to 20% of the project total. Other pros handle specialized work, such as design, electrical, plumbing, HVAC, and ensuring code compliance.
Labor rates vary by region, but expect $50 to $200 per hour for most skilled trades.
A designer or architect plans your layout, maximizes space, and ensures your conversion meets safety and building codes. Their expertise can be invaluable for complex or high-end conversions. Expect to pay $75 to $250 per hour or $2,000 to $10,000 as a flat fee for design services.
Electrical systems are among the most complex parts of a bus conversion. Electricians handle wiring, installing solar panels, battery systems, and generators. Electrician costs range from $50 to $130 per hour for electrical installation services. Professional work ensures safety and code compliance, reducing risks down the road.
Plumbers install fresh water and waste tanks, plumbing lines, fixtures, and manage the unique challenges of mobile water systems. Expect to pay $45 to $200 per hour for plumbing installation. Expert plumbing prevents leaks, clogs, and costly mistakes.
Depending on your bus conversion goals, you might also hire:
HVAC specialist: $1,000 to $2,000 for heating/cooling systems.
Painter or finishing specialist: $2 to $6 per square foot, or $20 to $50 for interior/exterior painting.
Countertop installer: $500 to $1,000 for new countertops
Solar installer: $3,000 to $12,000 for off-grid power systems
Interior decorator or organizer: $500 to $3,000 for maximizing storage and aesthetics
These professionals help with specialized systems or finishes and ensure a safe, comfortable, and attractive final product.
Where you live can significantly affect bus conversion cost. Labor rates are higher in urban areas and on the West Coast or Northeast, while rural areas and the Midwest often offer lower prices. Material availability, local regulations, and access to skilled professionals also play a role.
Regions with strict code enforcement or harsh climates (snow, humidity) may require additional upgrades, like better insulation or heating. Always check local requirements and market rates before starting your project.
Beyond the main phases, several other factors can influence bus conversion cost. Budget for taxes, insurance, and warranties, as well as ongoing expenses like maintenance, storage, and fuel. Optional upgrades—such as solar panels, ADA accessibility, or high-end appliances—add to the total. Repairs and post-construction cleanup also impact the bottom line.
Most conversions start with gutting the bus—removing seats, flooring, and old fixtures. This phase can cost $1,000 to $4,000, depending on how much needs to be removed and disposed of. Expect disposal fees for old materials and hazardous waste, such as insulation or fluids. Demolition is labor-intensive and can take several days to a week.
Bus conversions often require permits for DMV registration, building, plumbing, or electrical work. Homeowners are responsible for securing permits, but some contractors will handle this for you. Permit costs range from $100 to $1,000 per type, depending on location and project scope. Inspections ensure your conversion is safe and legal for use on the road or as a dwelling.
Many homeowners consider a DIY bus conversion to save on labor. You can save 40% to 60% on labor, but you’ll need skills in construction, electrical, and plumbing, plus plenty of time and patience. You’ll also need to pay for covering materials, tools, and equipment.
DIY can take six months to two years, depending on your schedule. Risks include mistakes, code violations, and safety hazards, which can end up costing more if you need to redo work or hire pros later. For complex systems or structural changes, it’s best to bring in professionals.
Remodeling a bus means making major structural changes—like altering the layout, adding or removing walls, or upgrading systems. Renovating involves refreshing an existing conversion, updating finishes, replacing appliances, or handling minor repairs.
Remodels cost more, often $30,000 to $100,000, while renovations can be as low as $10,000 to $25,000. Consider lifespan, code compliance, and the extent of changes needed when choosing between renovating and remodeling. Remodels are best for outdated or poorly designed buses, while renovations suit newer conversions that just need a refresh.
Looking to keep your bus conversion cost down? Try these money-saving strategies:
Source reclaimed or recycled materials.
Do some of the prep work or finishing labor, like painting, yourself.
Buy a bus in good mechanical condition to avoid costly repairs.
Plan and budget thoroughly to avoid scope creep.
Choose standard sizes for appliances and fixtures and limit custom features to essentials.
Shop around for materials and get multiple quotes from local home remodeling pros.
Consider phased upgrades over time.
Smart planning and resourcefulness can help you achieve your dream bus home without overspending.
A well-done bus conversion can increase the value of your asset, especially compared to traditional RVs or tiny homes. Your return on investment (ROI) depends on build quality, features, code compliance, and market demand. If your conversion is safe, efficient, and attractive, it can command a higher resale price.
However, bus conversions are niche, and financing or insuring them can be more challenging than for stick-built homes. Long-term value comes from durability, low maintenance, and the flexibility to use your bus for travel or as a unique living space.
Home is the most important place on earth, which is why Angi has helped more than 150 million homeowners transform their houses into homes they adore. To help homeowners with their next project, Angi provides readers with the most accurate cost data and upholds strict editorial standards. We extensively research project costs to develop the pricing data you see, so you can make the best decisions for you and your home. We rely on reputable sources, including the U.S. Bureau of Labor Statistics, academic journals, market studies, and interviews with industry experts—all to ensure our prices reflect real-world projects.
Want to help us improve our cost data? Send us a recent project quote to [email protected]. Quotes and personal information will not be shared publicly.
From average costs to expert advice, get all the answers you need to get your job done.
How much does a kitchen remodel cost? Find out the average cost and where you can save money on the path to building your ideal cooking space.
Knowing how much it costs to renovate a house will help you plan and budget appropriately. Use this guide to get a rough estimate for your project.
If your bathroom needs sprucing up, a new vanity will make a big difference. Vanity installation costs depend on the size and type of the countertops and fixtures you choose.
Explore acrylic shower wall pros and cons to decide if they’re right for your bathroom. Get the facts before your next remodel project.
Because the project takes place indoors, any time is the best time to remodel a bathroom. However, some factors influence scheduling and materials.
A living room that’s too big or too small can detract from value and utility. Learn about typical living room sizes to see if yours is just right.