Pre-Drywall Inspection Checklist: What’s Needed Before You Cover It Up
Make it right before sealing it tight


Before drywall goes up in a new home, it's the last chance to ensure everything under the hood is in good shape. That’s why an in-depth pre-drywall inspection checklist is critical. It ensures that all those behind-the-scenes components are properly installed, in good working order, and up to code before they’re hidden behind your new interior walls.
Whether you’re building a new home or managing a new construction project, this type of home inspection should never be skipped. From catching mistakes early to giving everyone some much-needed peace of mind, each area of this inspection is crucial, so we’re going to break down what needs to be checked and why it matters.
Why Is a Pre-Drywall Inspection Needed?
The whole point of a pre-drywall inspection is to make sure all of the structural elements of the house and its critical systems are in good shape before the walls are sealed. Once that drywall goes up, it’s much more difficult—and costly—to identify and repair issues.
This inspection step can identify problems that went unnoticed during previous construction phases, and many of these issues can cause real problems down the road. By understanding what’s on a pre-drywall inspection checklist and why, you can avoid construction delays as well as expensive repairs or failed home inspections in the future.
Structural Inspection
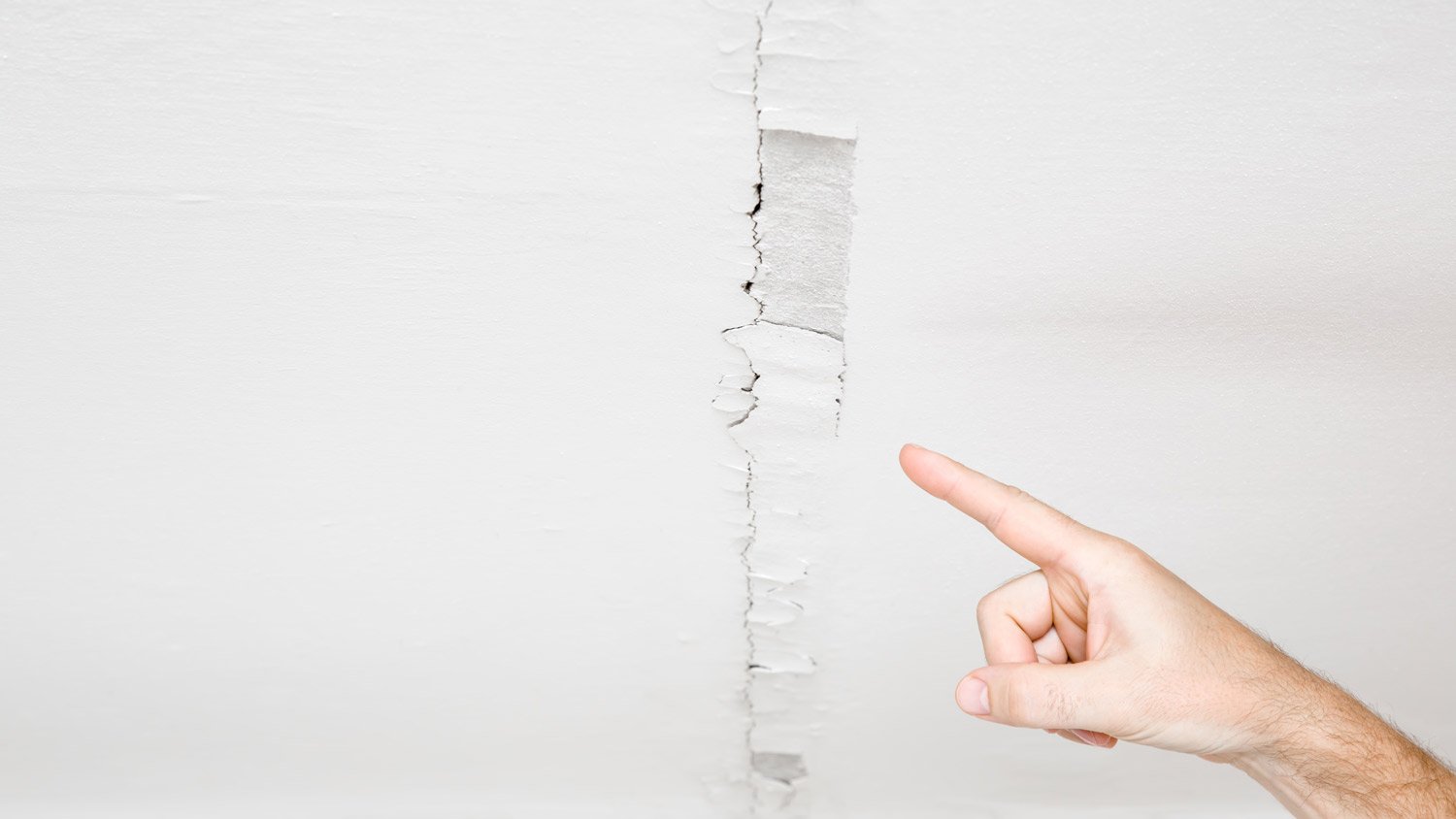
Structural elements are the foundation—literally—of the home. If foundational aspects aren’t in good order, it can have damaging effects. Here are some items to check in a structural inspection:
Foundation: Make sure there are no cracks, moisture problems, inconsistencies, or other signs of issues in the foundation slab or basement walls.
Framing: Verify that framing is level, precise, and correctly spaced for both drywall installation and overall structural support.
Windows and doors: Confirm that all doors and windows are correctly installed, square, and sealed with no gaps.
Support beams and load-bearing walls: Ensure all structural supports are placed correctly and secured properly.
Roof: Look for signs of improper roof installation like leaks or sagging, which can affect insulation and structural integrity.
Attic: Make sure the attic’s framing is complete and accessible, and confirm that there’s space for insulation and proper ventilation.
Electrical Inspection
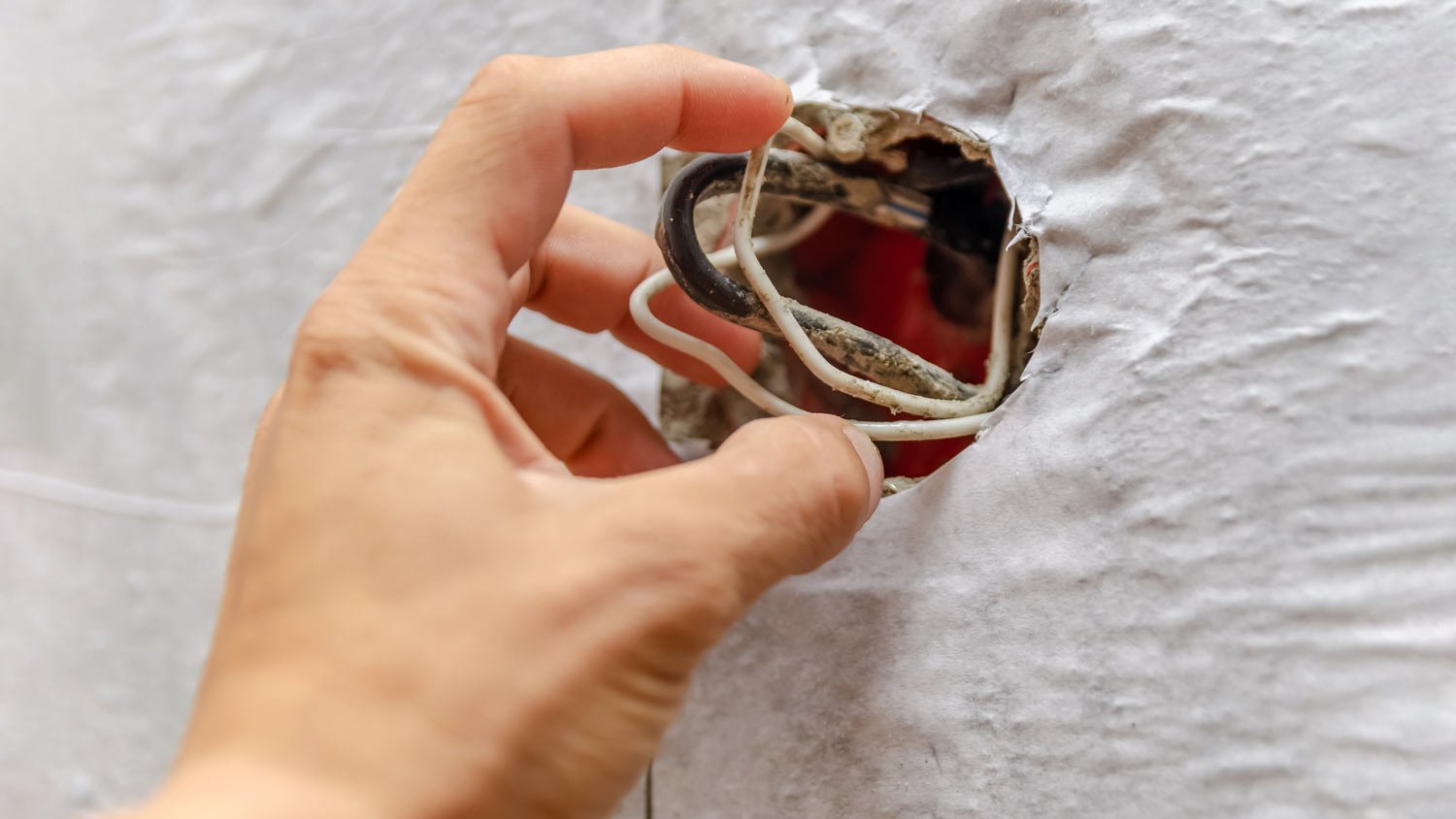
During the electrical inspection, all electrical components are checked for safety, accessibility, and code compliance. These are some of the elements inspected to identify possible signs of electrical problems in the future:
Wiring: Ensure all wiring is properly routed, clearly labeled, and securely fastened.
Outlets and switches: Confirm that outlet and switch boxes are installed correctly at the ideal location and height.
Junction boxes: Make sure junction boxes are easily accessible and not overcrowded with wires.
Electrical panel: Check that the panel is fully and correctly installed, with circuits wired properly and breakers labeled.
Plumbing Inspection
Plumbing errors can cause big issues down the road. So, before the walls go up, it’s important to confirm that these systems are correctly installed and free of leaks. Here’s what needs to be checked:
Water supply: Check that hot and cold water lines are installed properly and that they are pressure-tested for leaks.
Drainage: Examine drain lines for efficient waste flow by ensuring proper slope and secure attachment.
Pipe placement: Verify that pipes don’t interfere with framing or other systems and have proper clearance.
Venting: Make sure plumbing vents are correctly in place and that they extend correctly through the roof.
Dishwasher: Check that dishwasher drain hoses and water lines are correctly installed and easily accessible.
HVAC Inspection
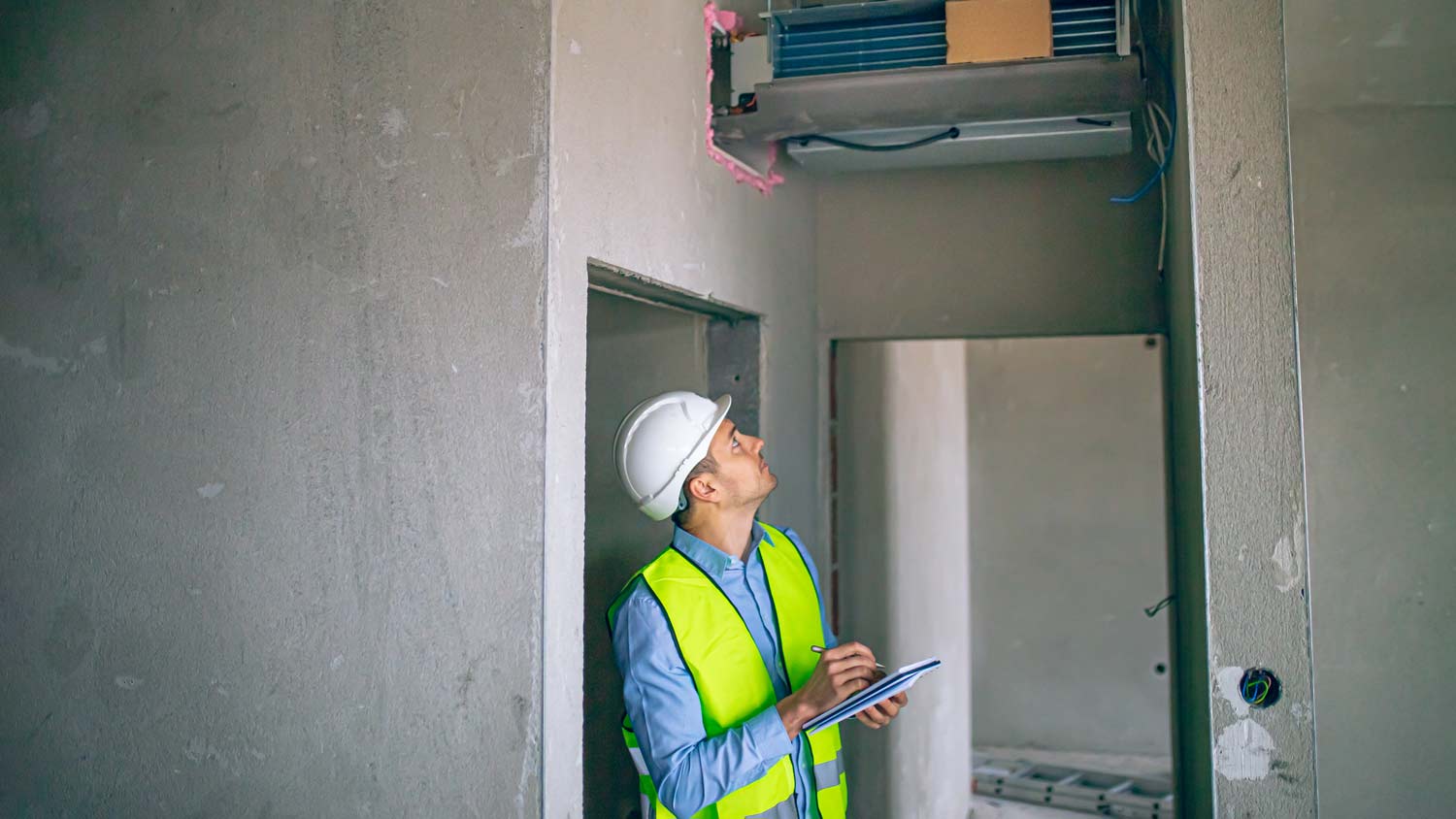
Many HVAC elements live behind the walls and ceilings, so it’s important to inspect them for compliance and efficiency before the drywall goes up. Here’s what’s examined:
Ductwork: Make sure ducts are securely attached, properly routed, and have adequate insulation around them.
Vents and returns: Verify that all vents and return registers are properly placed and sealed and that they will remain unobstructed when the walls go up.
HVAC system: Confirm that the furnace or air handler is installed correctly and lines are run cleanly without leaks.
Flooring, Walls, and Ceiling Inspection
Before the drywall covers the walls and ceiling, there are some checks on these areas and the flooring that should be performed:
Subfloor: Examine the subfloor for creaks, weak spots, or gaps that could affect the integrity of the flooring later.
Insulation: Make sure all ceiling spaces and wall cavities are adequately insulated and check that the insulation materials aren’t improperly placed or compressed.
Firestop materials: Confirm that the fire-blocking materials are installed to code in order to prevent the spread of fire within wall cavities and ceiling voids.
How Much Does a Pre-Drywall Inspection Cost?
A pre-drywall inspection costs between $200 and $400, with an average cost of $300. This cost depends on a few elements, including the complexity and size of the home. This isn’t an unnecessary extra expense. The price of skipping this inspection could end up being much higher if issues aren’t identified before drywall goes up.
Hiring a drywall pro near you for this comprehensive inspection minimizes costly surprises later and could save you thousands in future repairs or remodels.
The time it takes to complete a pre-drywall inspection depends on the size of the home as well as the complexity of its build. Most take between one and three hours, but large custom homes or those with complicated HVAC, electrical, or plumbing systems take even longer. Your inspector will examine each room and each system in detail to make sure everything is properly installed and up to code.
All essential mechanical systems should be completely installed before drywall goes up. This includes wiring for electrical systems, pipes and vents for plumbing systems, and ductwork, framing, fire-blocking, and insulation for HVAC systems. Prior to drywall installation, it’s important to ensure these systems have passed local code requirements. Once the walls go up, access to most essential systems is complex, costly, and labor-intensive.

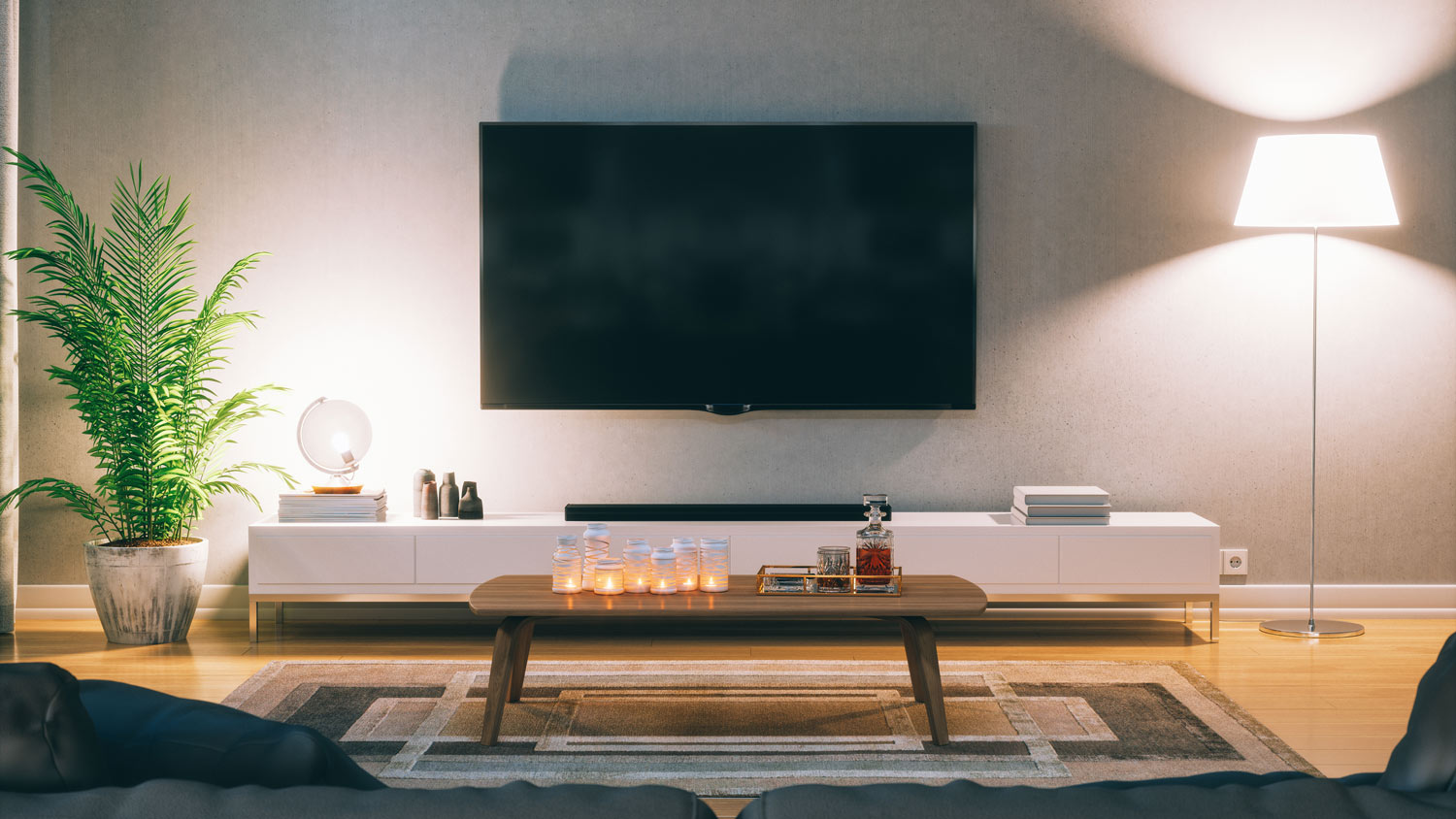
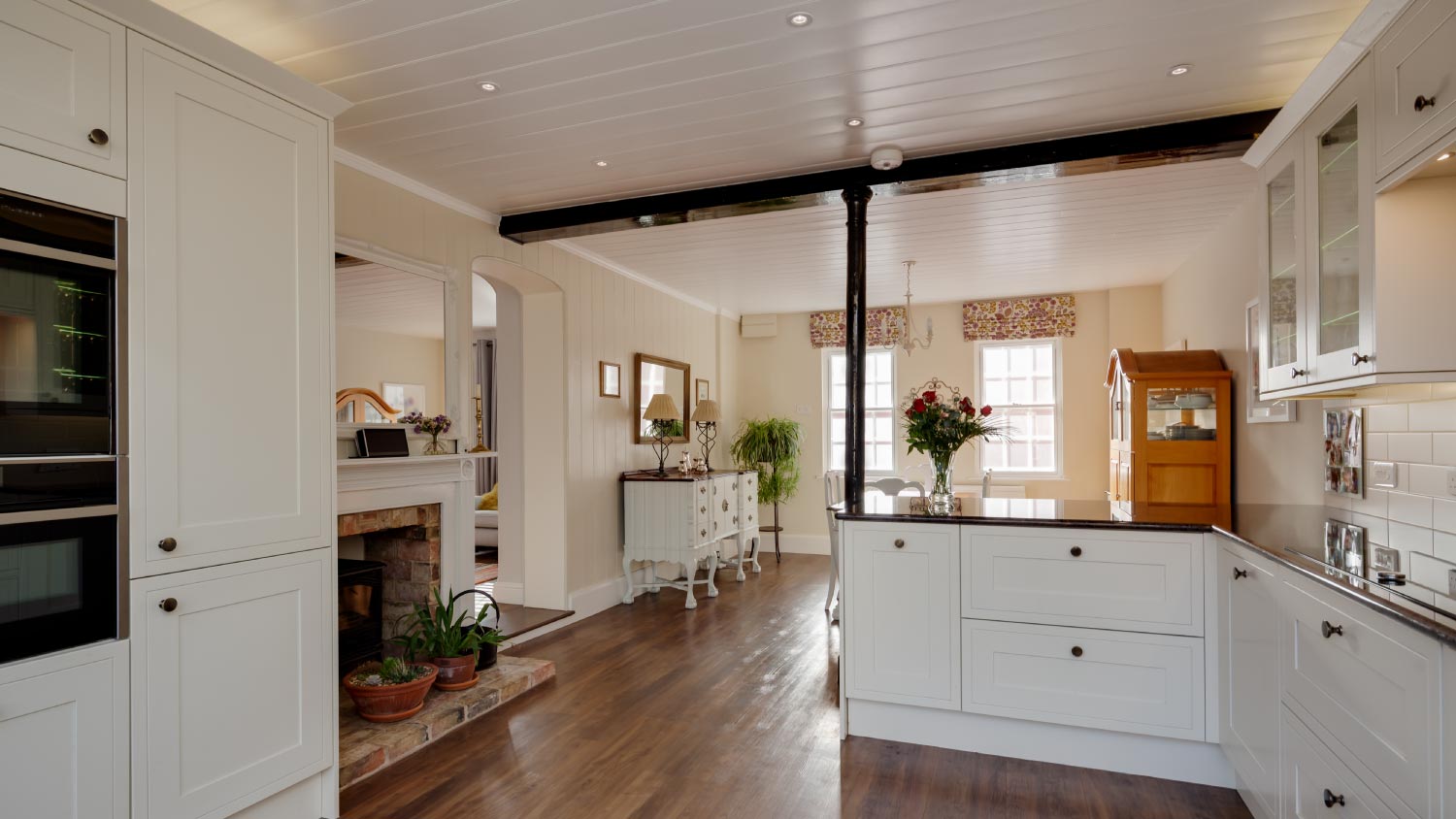
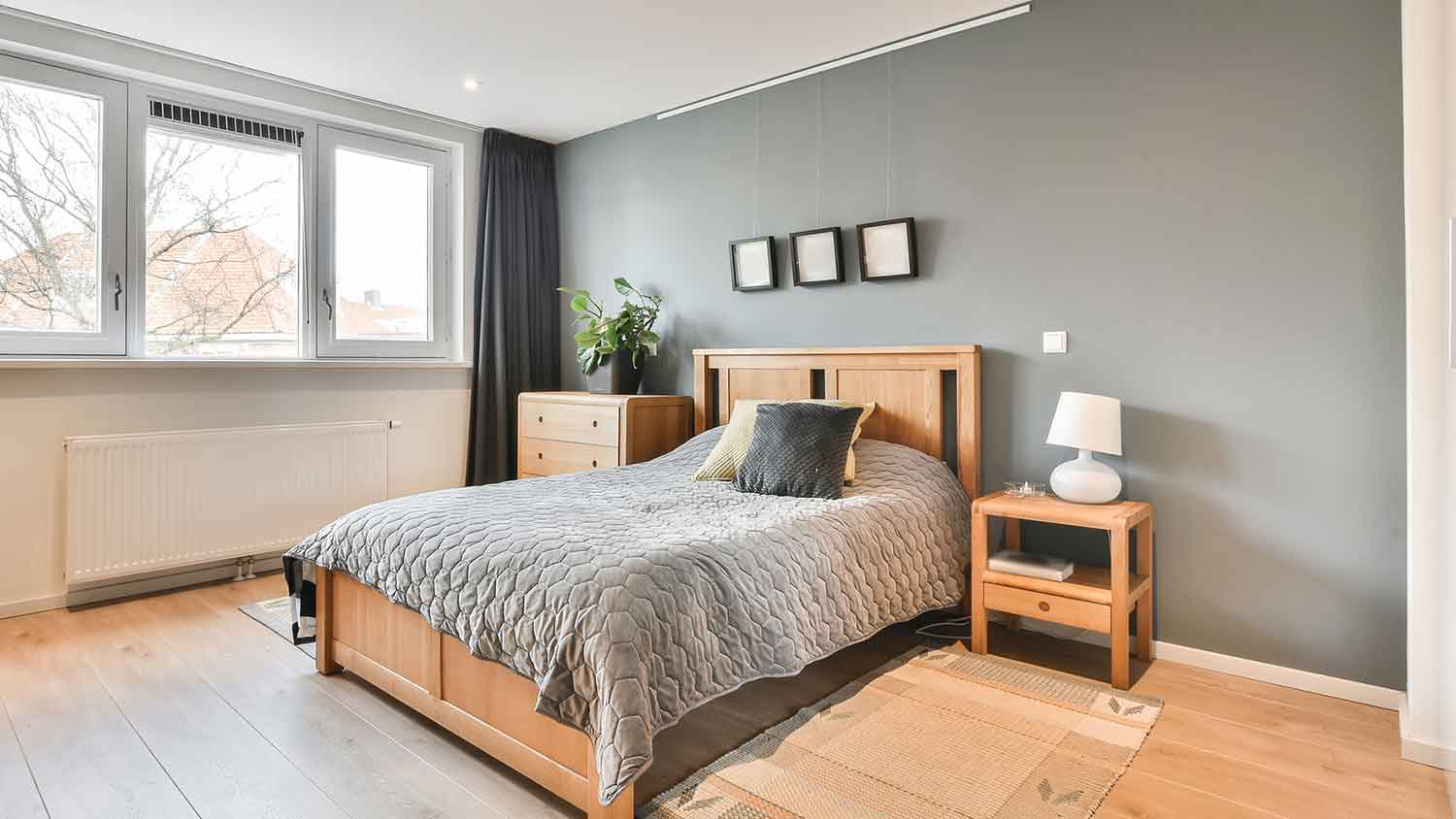
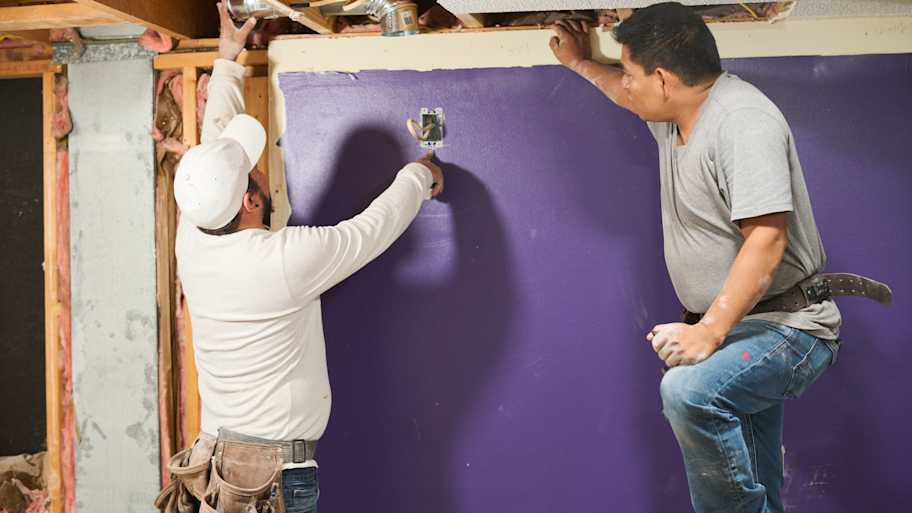