How Much Does It Cost to Wrap Dock Pilings? [2025 Data]
The cost to wrap dock pilings averages $3,800, with most homeowners paying between $2,250 and $5,250. Prices vary based on piling size, material, and labor rates.
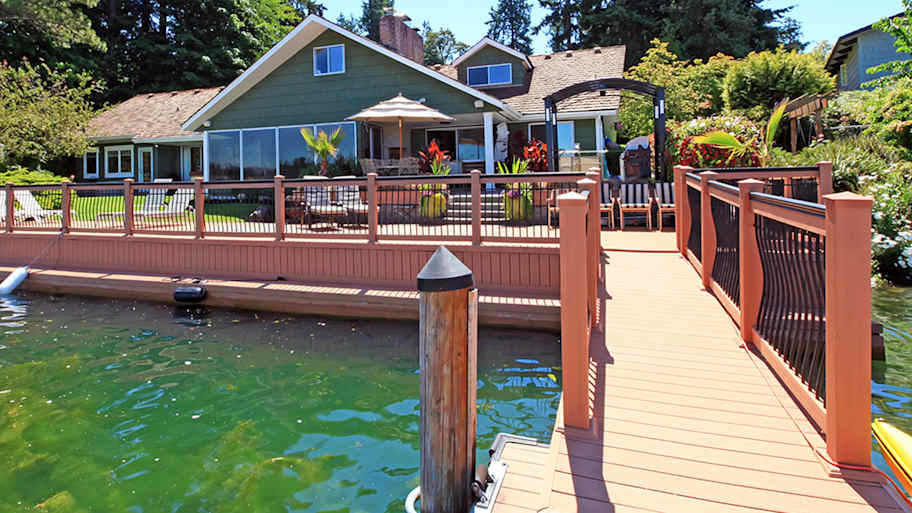
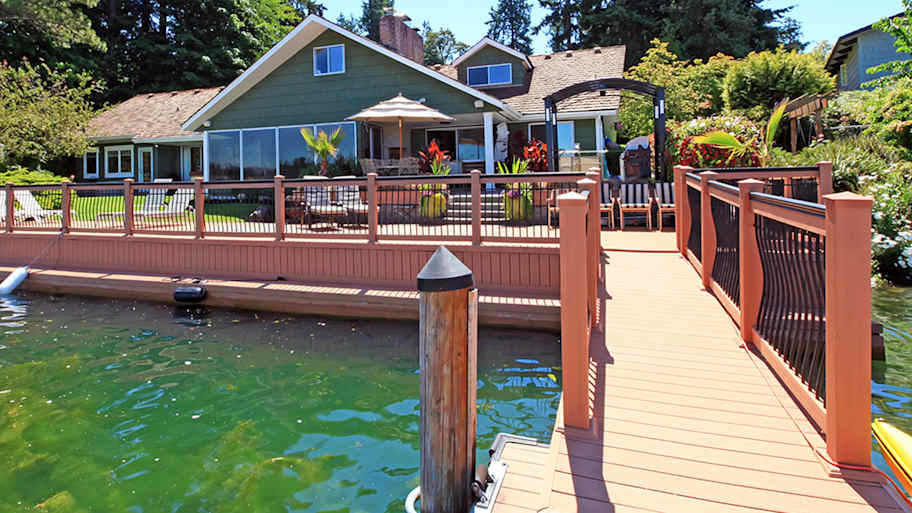
Wrapping dock pilings protects against marine borers and rot.
Material type and piling size are the biggest cost drivers.
Professional installation, costing $50 to $120 per hour, ensures long-lasting protection.
Maintenance and warranties can impact total ownership costs.
Upgrading piling wraps can extend the lifespan and value of a dock.
This article was created using automation technology and thoroughly fact-checked and edited by an Angi Editor in accordance with our AI policy.
The cost to wrap dock pilings ranges from $900 to $8,400, with an average project cost of $3,800. Homeowners can expect to pay between $15 and $35 per linear foot, depending on the size and number of pilings, material choice, and labor rates. Investing in piling wraps helps protect your dock from marine pests and prolongs its lifespan.
Whether you’re looking to preserve your waterfront investment or prevent costly repairs, understanding the cost to wrap dock pilings can help you plan confidently. Let’s walk through the details so you know what to expect.
Cost by Size of Dock Piling Wrap
The size and number of dock pilings are major factors in the total project cost. Larger or more numerous pilings require more material and labor, resulting in increased expenses for both supply and installation. Most residential dock pilings are between eight and 12 inches in diameter and range in height from 10 to 20 feet. To estimate your total cost, you’ll need to calculate the combined linear footage for all pilings.
For example, wrapping ten pilings that are each 12 inches in diameter and 15 feet tall requires more material and time than wrapping six pilings of eight inches in diameter. The total linear feet is calculated by multiplying the number of pilings by their height.
Piling Size (Diameter x Height) | Number of Pilings | Total Lin. Ft. | Estimated Cost Range |
---|---|---|---|
8" x 10' | 6 | 60 | $900–$2,100 |
10" x 15' | 10 | 150 | $2,250–$5,250 |
12" x 20' | 12 | 240 | $3,600–$8,400 |
Dock Piling Wrap Cost by Type
Choosing the right wrap material affects durability, appearance, and cost. Common materials include PVC, HDPE, vinyl, and composite wraps. Thickness (measured in mils) and resistance to UV, saltwater, or marine pests also vary. Thicker, higher-grade wraps last longer and cost more upfront, but can offer better long-term protection.
Some wraps are better suited for saltwater environments, while others perform well in freshwater. Consider lifespan, flexibility, and ease of installation when selecting a material.
Wrap Material | Thickness | Cost per Lin. Ft. | Durability (Years) | Pros | Cons |
---|---|---|---|---|---|
PVC | 60–120 mils | $15–$22 | 10–20 | UV resistant, flexible, affordable | Can puncture if thin |
HDPE | 80–150 mils | $18–$28 | 15–25 | Strong, impact-resistant | Less flexible, higher cost |
Vinyl | 40–80 mils | $14–$20 | 8–15 | Easy to install, budget-friendly | Shorter lifespan |
Composite | 100–200 mils | $25–$35 | 20–30 | Longest lifespan, low maintenance | Most expensive, limited colors |
Cost by Location
Where you live significantly affects the cost of wrapping dock pilings. Coastal areas with more marine contractors may offer competitive pricing, but stricter regulations can increase permit and inspection fees. Inland or remote locations might see higher costs due to limited contractor availability and mobilization fees. Local environmental requirements and labor rates also play a role in total project cost.
Dock Piling Wrap Installation Cost Factors
There are several factors to consider when budgeting to wrap dock pilings, including labor, permits, and additional expenses.
Labor
Labor is a major part of the cost to wrap dock pilings. Most projects require marine contractors or experienced dock builders. Labor charges may be by the hour or per linear foot, with rates ranging from $50 to $120 per hour or $7 to $18 per linear foot for installation.
Factors such as water depth, limited dock access, and project complexity can increase labor costs. Regional labor rates also influence your final bill.
Permits
Many locations require permits for dock work, including piling wraps. Permit fees range from $50 to $500, depending on your jurisdiction and the project’s size. In some areas, you may also need to pay for inspections or submit engineering plans, which can add to your timeline and budget. Always check with your local marine or building authority before starting.
Additional Features
Optional upgrades can enhance performance but also add to the cost of wrapping dock pilings. Anti-fouling coatings, reinforced or double-layer wraps, and integrated pest barriers can improve protection. Custom colors or UV-resistant finishes are available for those wanting a specific look or added durability. Each add-on increases the initial investment but may offer long-term benefits or reduced maintenance costs.
Service Add-Ons
Other factors that can impact your project cost include the total number of pilings, water depth, and dock accessibility. Preparing the site—such as cleaning pilings or removing old wraps—can add labor hours.
Delivery and mobilization fees may also apply for remote or hard-to-reach docks. After installation, expect possible charges for debris disposal, post-installation inspection, or engineering design if your project is custom or complex.
Additional Costs to Consider
Several factors can impact the long-term cost of your project, including warranties, insurance, and maintenance.
Warranties
Many manufacturers and installers offer warranties on dock piling wraps. Manufacturer warranties often cover defects in materials, while installer warranties address workmanship. Warranty periods range from five to 25 years. Choosing a longer or more comprehensive warranty may increase upfront costs, but can offer peace of mind and potential long-term savings if issues arise.
Maintenance
Maintaining your dock piling wraps is essential for lasting performance. Cleaning off algae, barnacles, or debris should be done at least once a year, with costs ranging from $100 to $300 annually for professional cleaning. Watch for signs of wear, such as tears or loose edges, and schedule repairs as needed to prevent further damage.
Insurance
Upgrading your dock piling wraps may affect your homeowners or marine insurance. Some insurers offer reduced premiums for improved dock protection, but they may require proof of professional installation. Always confirm with your provider to understand how piling wraps impact your policy.
DIY Dock Piling Wrap vs. Hiring a Pro
Some homeowners consider wrapping their own dock pilings to save money. DIY material costs range from $10 to $20 per linear foot, and you’ll need tools like utility knives, marine-grade fasteners, and safety gear.
While you can save on labor, DIY installation is physically demanding, requires working near or over water, and can void warranties if not done correctly. Hiring a local dock professional ensures proper installation, safety, and eligibility for warranties, especially for docks in deep or moving water.
Installation Method | Average Total Cost | Labor Hours | Pros | Cons |
---|---|---|---|---|
DIY | $1,000–$3,000 | 20–40 | Lower cost, personal satisfaction | Safety risks, no warranty, and time-consuming |
Professional | $1,200–$5,000 | 8–16 | Expert quality, warranty coverage | Higher price, must schedule with the contractor |
Dock Piling Wrap Replacement vs. Repair
Knowing when to repair or replace dock piling wraps protects your investment. Small tears or loose sections can often be repaired for less, especially if the material is still within its expected lifespan and under warranty. If the wrap is extensively damaged, worn out, or nearing the end of its life, replacement is the better choice. As a rule, if dock repair costs exceed 50% of replacement costs, opt for a full replacement.
Repairing a piling wrap costs $10 to $18 per linear foot, while full replacement ranges from $15 to $35 per linear foot and includes removal, new materials, and installation. Replacement is often the most cost-effective option if your dock is older or has widespread damage.
Does Wrapping Dock Pilings Add Value to Your Home?
Investing in dock piling wraps can be a smart move for waterfront homeowners. Wrapping pilings extends the life of your dock, reduces the need for costly repairs, and can improve your property’s value.
Compared to other dock upgrades, piling wraps offer a high return on investment by preventing structural damage, which can be expensive to fix. They also enhance safety and functionality by keeping your dock stable and visually appealing. Enhanced curb appeal is a valuable added bonus for those looking to sell or simply enjoy a well-maintained waterfront property.
Tips to Reduce Costs While Wrapping Dock Pilings
To keep your project budget-friendly, consider the following tips:
Get multiple quotes from marine contractors to compare pricing.
Schedule installation during the off-season to take advantage of potential discounts.
Choose standard wrap materials and sizes to avoid custom upcharges.
Bundle piling wrap with other dock maintenance projects to save on mobilization fees.
Perform basic site prep (e.g., cleaning pilings) yourself to reduce labor hours.
Consider long-term value and warranty when selecting materials.
How Angi Gets Its Cost Data
Home is the most important place on earth, which is why Angi has helped more than 150 million homeowners transform their houses into homes they adore. To help homeowners with their next project, Angi provides readers with the most accurate cost data and upholds strict editorial standards. We extensively research project costs to develop the pricing data you see, so you can make the best decisions for you and your home. We rely on reputable sources, including the U.S. Bureau of Labor Statistics, academic journals, market studies, and interviews with industry experts—all to ensure our prices reflect real-world projects.
Want to help us improve our cost data? Send us a recent project quote to [email protected]. Quotes and personal information will not be shared publicly.


